CO2 – amongst other global warming gases such as methane, water vapor, NOX – is a major by-product of the energy generation using fossil fuels. A report published by the Intergovernmental Panel on Climate Change (IPCC) details the impacts of global warming of 1.5° C above the pre-industrial level. The report also discusses the sustainable mitigation pathways to be followed in the next 10 years to reach zero greenhouse gas emission in different sectors of the economy such as electricity, manufacturing, agriculture, etc. within 50 years. Countless debates on climate change have resulted in rapid mitigation strategies to reduce CO2 emission to keep the temperature rise in check. However, with the growing population and growing wealth, the demand for energy increases proportionately. This simply means more CO2will be generated to meet our future demands unless promising technological measures are undertaken.
What can be done for a greener future?
Using alternative renewable energy is a viable option to circumvent the CO2 problems, but the industrial process required for the realisation of these technologies contributes to the carbon footprint. So, what can be done about this?
One of the most efficient strategies would be to capture and store the CO2 (the process referred to as carbon capture and sequestration) so that it can be converted to valuable products such as chemical fuel or industrial raw materials. This approach allows us to achieve a carbon-neutral lifestyle without compromises.
The need to capture large quantities of CO2 efficiently is associated with exxagerated costs which act as a barrier to the industrial realisation of carbon capture and storage technologies (CCS). Besides that
- Usually 2/3 of the cost involved in the CCS technology is devoted to CO2 capture. This leaves little left for the conversion of the adsorbed CO2 to value-added products. Therefore, the capturing CO2 limits its implementation from an economic standpoint.
- Currently, the power plant industry uses alkanolamine solutions to capture CO2 (from the combustion of fuel). However, the regeneration of the alkanolamine is energy intensive.
- Alternatives such as activated carbon, zeolites, and porous polymers, etc. are widely used but are unable to keep up with the rate of CO2 generated from a variety of industries.
How and why can MOFs help with capturing CO2?
MOFs prove to be powerful and promising candidates in fighting CO2 emissions as they exhibit the following
- A porous structure resulting in an enormously large surface area (several 1000 m2 per gram MOF)
- Solid in nature which results in the ease of handling
- tuneable pore size for selective adsorption of gases from gas mixtures
- tuneable physicochemical properties that match the adsorbed gases
- modifiable functional groups for selective adsorption adsorbtion of gases
In other words, metal-organic frameworks selectively adsorb molecules from gaseous media and regenerate the captured gas.
“Regeneration of metal-organic frameworks requires only a fraction of the energy that zeolites or silica require”
Many MOFs have the capability of capturing carbon dioxide, but the uptake varies. Here is a shortlist of well-known and lesser-know, better and worse MOFs and their uptake capability. These are measured at standard conditions (1 bar, 24° C).
MOF | CO2 Capacity (mmol/g) |
HKUSt-1 | 4.1 |
PCN-66 | 26.3 |
PCN-88 | 7.1 |
MOF-74 (Zn) | 5.5 |
MOF-74 (Ni) | 5.8 |
MOF-74 (Co) | 7 |
The regeneration of metal-organic frameworks to release the CO2 from the adsorbent requires only a fraction of the energy that zeolites or silica require, making it a very energy efficient process. Not to mention commonly used amine scrubbing, which requires significant energy to release the chemically bonded CO2 from the amine solution. Furthermore, MOFs have proven to carry out robust CO2 adsorption even in the presence of water molecules, which is present in significant concentration in some flue gas streams.
On the contrary, zeolites show compromised CO2 adsorption in the presence of water. On the downside, MOFs are not yet as temperature-resistant as zeolites.
We take a more in-depth look at capturing CO2 in our case study:
Given the strong adsorption properties and easy regeneration of the MOF material, the adsorbed CO2 can thus be converted into value-added products. We think of CO2 synthesis to methane or methanol, which can be used to fuel gas-powered cars or for cooking devices. Specific metal-organic frameworks work as catalysts for the methanation of CO2. Or up-cycle the captured carbon into plastic for the production of sustainable products (maybe not for plastic straws).
Flexible MOFs – the next-generation contenders for CO2 adsorption efficiency
Conventional porous MOF materials such as HKUST-1, MOF-74-M (M for metal such as cobalt, nickel, magnesium, manganese), and MIL-100 (Fe) have been reported to exhibit competitive CO2 adsorption capacities. Even some MOFs such as the NU-100 have been characterized to have an astounding CO2 adsorption capacity as high as 2315 mg per gram of MOF material. That is 10x more than zeolites adsorb (CO2 adsorption capacity of zeolite 13X is 185.4 mg of CO2 per gram of the material). The rigid pore structure of the first-generation MOFs can collapse when the CO2 is removed for further processing. This is where the ‘flexible MOFs’ gain colossal interest.
CO2 adsorption of MOFs is 10x higher than of zeolites
Flexible MOFs are MOFs which undergo structural changes upon temperature or/and pressure variation (they are sometimes called ‘breathing’ MOFs, comparing it to the chest when breathing in and out). As a result, the CO2 adsorption capacity of these MOFs substantially increases and therefore, making them an attractive candidate. The flexible nature can be simply achieved by using appropriate building blocks and structural design that prevents the MOF from collapsing upon the departure of gas molecules from their pore.
Of some 20,000 reported MOFs, only about 100 of them feature the flexible behaviour. Recently, MOF researchers discovered an Indium-based MOF (Me2NH2)[In(ABDC)2], SHF-61, which shows selective adsorption of CO2 and Methane CH4 depending on the ‘breathing status’ of the material. The CO2 adsorption capacity of this MOF was reported to be 2.4 mmol per gram of MOF material.
CO2 adsorption from biogas industry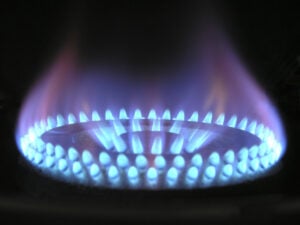
In 2014, nearly 14% of the total final energy consumption globally was generated using biogas. Biogas is generated from biodegradable matter such as animal waste, food waste, sewage, etc. are converted to methane and CO2. While we use methane for different applications including heating, driving our vehicles, chemical production, etc. the side-product CO2 is deadly for the environment because of its heat-trapping nature. This calls for a vigilant separation of these gases to protect our environment and also to improve the process economics by transforming undesirable side-yields into value-added products.
Membrane technology is widely used for industrial gas separation. While the membrane-based separation is cost-effective, there are certain disadvantages when it comes to CO2 separation. For instance, membranes require low concentration of CO2 to prevent it from swelling and resulting in irreversible damage. However, power plants usually generate flue gas stream with a high concentration of CO2. Reducing the concentration can be difficult. In contrast to the membranes, MOFs are suitable candidates to overcome this hurdle. They have a porous structure with a very high surface areas that allows for effective separation and storage.
Researchers have shown that Zn-based MOF of different morphologies (rod and plates) possess different surface pore aperture. By carefully controlling the synthesis, suitable morphology can be chosen to maximize the methane adsorption over carbon dioxide (CO2). This MOF could be used to effectively produce methane gas and capture the toxic side-product CO2.
What about reducing other global-warming agents and harmful gases?
The most commonly used agents in cooling applications (Chlorofluorocarbons (CFCs) and hydrochlorofluorocarbons (HCFCs)) are often not environmentally benign and have thus been declared global warming agents. Moreover, the CFCs have strong effects on ozone depletion, which is undesirable. Efficient adsorption-based cooling systems depend on the adsorbate-adsorbent pairs. Recently, researchers have discovered that the MOF/fluorocarbon pair can be used for adsorption cooling applications in an environmentally-friendly way. For this, they have engineered the pores of Ni-based MOF-74 which now allow higher water and fluorocarbon (R134a) uptake.
Talking of harmful gases, upgrading gas tanks with MOFs will increase their capacity up to 3x and offer sub-atmospherical storage.
Wrap-up
The alarming rate of CO2 generation requires a great deal of attention and audacious solution by recruiting unconventional and promising materials such as MOFs. On the bright side, the industries have begun to direct their interests towards MOFs by trying to realize their potential in Carbon Capture and Sequestration through implementation in pilot plants. To us, this instills the confident vision that MOF production will soon be scaled-up to meet the demands of carbon-intensive energy sectors. Besides, it wouldn’t be surprising if MOFs are employed in the near future for scrubbing other industrial gases to turn them into valuable products, given the current trends and positive outcomes of MOF research.