Carbon capture and storage are urging novel technologies to increase current capture capacity and a more economical alternative than amine scrubbers. Recent efforts in this field have been directed towards the use of solid sorbents, in particular for post-combustion capture. Among solid materials used for CO2 capture, calcium-based materials and Metal-Organic Frameworks have attracted attention in the last decade. In this blog, we aim to compare their pros and cons.
What is calcium looping technology?
The calcium looping (or Ca-looping) process is a type of chemical looping which uses calcium-based compounds such as CaO (usually derived from limestones) for carbon capture through a reversible chemical reaction. The process consists of two steps, carbonation, and calcination. In the carbonation step, CaO reacts with the CO2 in the flue gas stream, forming CaCO3. Then, the calcium carbonate is transferred to another reactor for the calcination step, where the reverse reaction is carried out to obtain a pure carbon dioxide stream.
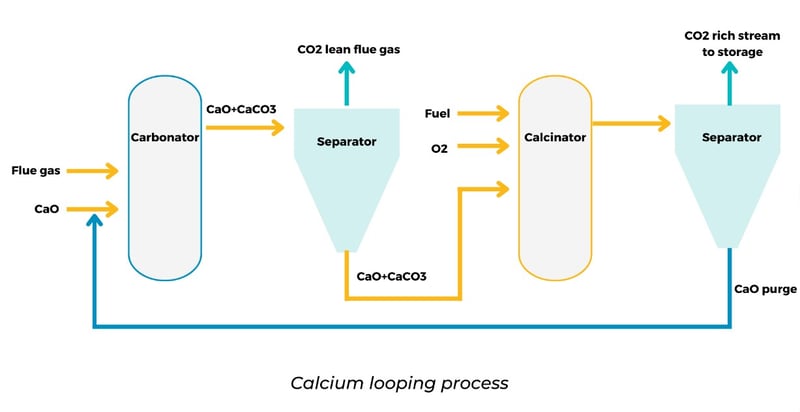
The material sorbent used in this process is cheap and widely available. Also, calcium materials have a particular affinity toward sulfur compounds. Therefore, Ca-looping will result in partial desulphurization. Besides, waste material after carbon capture processing has potential use in other industries like cement, which can be used as a feedstock.
However, Ca-looping also has some disadvantages. For instance, the carbonation and calcination steps are temperature dependent and require high temperatures. The carbonation process is carried out at between 650-700°C, while the calcination at 900-950°C. Therefore, the whole process is energy-intensive. Also, the conversion rate from CaO to CaCO3 decreases upon cycling due to compaction at high temperatures and competing sulphation/sulphidation reactions. Ca-looping systems are still under development since they require improved material stability during operation to avoid material loss after a few cycles.
MOFs as alternative sorbents
Metal-Organic Frameworks (MOFs) are hybrid materials consisting of metal nodes and organic linkers. MOFs possess well-defined three-dimensional microporous structures with very high surface areas. They can be synthesized in a controlled manner by manipulating their components. Owing to their particular properties of easy design, synthesis, and tunning, they have shown improved selectivity towards CO2 in post-combustion carbon capture.
MOFs perform carbon dioxide capture through a combination of adsorption and physical separation. In the adsorption phenomena, CO2 is bounded to the surface of the MOF material through weak chemical interactions, while other contaminants can be separated by size exclusion. Recent advances in MOFs for carbon capture have shown that these materials can be used in real flue gas conditions with promising results and good stability.
Just like Ca-looping, the implementation of MOFs for CO2 capture arose to overcome the disadvantages of amine scrubbing, such as high energy consumption and amine degradation. Since MOFs can be modified at will, they can be fabricated to exhibit similar reactivity to liquid amines by introducing amine molecules to their structure. In this way, MOFs can exploit the advantages of amines meaning high reactivity towards CO2 and the stability of a robust structure. For instance, amine-modified MOF materials can achieve capture capacities up to 4.6 mmol/g and retain their performance in humid conditions after several adsorption-desorption cycles.
MOF systems for improved energy efficiency
MOF-based systems for carbon capture are operated using typical swing adsorption-desorption methods like temperature and pressure swing.
Unlike calcium materials, MOFs only require mild temperatures for regeneration, below 100 °C
The low energy requirement of MOF-based systems put them ahead of calcium looping in the energy consumption area. Besides the low energy consumption of MOF-based systems, compared to calcium materials, they show higher stability under typical operating conditions.
Due to its energy-intensive nature, calcium looping is only favored to be implemented in certain facilities like those for the Natural Gas Combined Cycle, where residual heat can help reduce the energy efficiency penalties for the whole carbon capture process. Moreover, synthetic CaO materials are required in those cases to achieve acceptable efficiencies, increasing sorbent costs.
MOF materials offer different advantages for carbon capture processes:
- High selectivity
- Thermal stability
- Low energy requirements
Due to these properties, MOFs are considered one of the most promising technologies for replacing amine-based absorbent, the current primary method used to perform carbon capture at the industrial scale.
Please visit our previous blogs and success stories to learn more about MOFs' amazing world.