The applications of metal-organic frameworks are diverse:
- Gas storage (e.g. hydrogen, methane, toxic gases)
- Gas purification
- Gas capture (e.g. Carbon dioxide, volatile organic compounds)
- Gas sensing
- Photo- & electrocatalysis
- Semiconductors
- Drug delivery
- Biomedical sensing and imaging
- Dehumidification
- Water treatment
Other porous materials such as activated carbon, zeolites and silicas are already being used in many of these applications. These materials are very well-known in academia and industry – no wonder, they exist for quite some time now (activated carbon has been used for centuries, silica already at the beginning of the 19th century and zeolites had their first commercial applications in the middle of the 19th century). Their prices range from several hundred dollars to above 2500$ per metric ton. You can even get them from Alibaba or Amazon – fast delivery within several days or weeks.
These materials are all great in what they do, but certainly have their shortcomings as well. Activated carbon does a great job at basic filtration. However, it’s rather unselective in what it adsorbs. For regeneration – mainly thermal reactivation (a.k.a. burning it out) – it requires a large amount of energy and captured materials cannot be recycled into value added products.
There are more than 200 forms of zeolites researched and produced until now, while there could be around thousands more that just haven’t been synthesised yet. The 300 available zeolites have been studied to a great extent and are well-understood in academia and in the industry. This is just a fraction compared to the documented 300’000+ MOF structures in the Cambridge Structural Database. And MOFs close many gaps that are left open by other porous materials.
Cost vs. benefit – Taking the whole process into account
High performance comes at a cost – higher performance of your product also increases your potential selling value. When evaluating MOFs for an application, it’s important to take all cost drivers into account – in other words: the total cost of ownership. This includes costs such as equipment, depreciation, maintenance and repairs and energy consumption of your product or service.
Let’s have a look at an adsorption/filtration solution, based on activated carbon. Activated carbon comes at competitive prices, but it is rather unselective in what it adsorbs and uptake capacity is limited. So you need a lot of material to do the job. Furthermore, the filters fill up and are energy-intensive to reactivate; you either need to replace the filters regularly or you need to reactivate them at very high temperatures. In the first case, you have recurring low cost for the material and – depending on the design – noticeable downtime during the replacement. This is an economic cost itself and a value-decreasing aspect for the end-consumer. In the latter case you need heaps of energy, another cost driver.
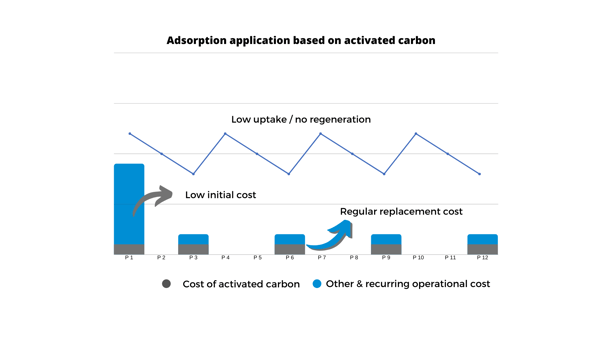
If the activated carbon is regenerated instead of replacement, it requires temperatures of up to 900°. Given the ease of production of activated carbon and the low cost of raw materials, the initial costs are very low. However, regular downtime due to filter replacement is an economic cost in itself.
If you use Zeolites or Silica for a comparable adsorption process, the material usually has a long lifetime and can be regenerated while still offering competitive material pricing. The uptake capacity is higher than the one of activated carbon in many cases. Nonetheless, the regeneration process is energy-intensive and therefore results in higher operating costs.
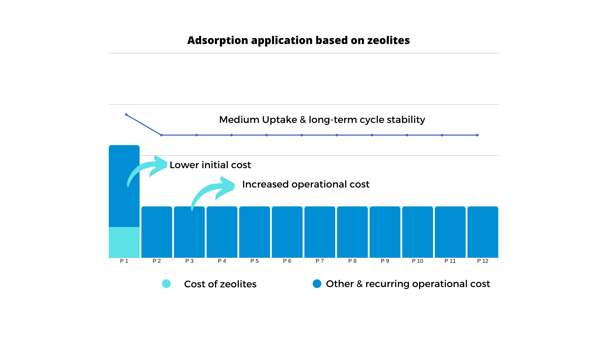
Zeolites are very stable for multiple cycles, which reduce the overall amount of material required for the application. The energy required to regenerate Zeolites can be rather higher due to the strong bonds between adsorbent and adsorbate.
What if the filtration material costs more initially, but
…reduces downtime and energy-consumption?
…doesn’t need replacement even after thousand cycles?
…is highly selective and therefore increases the quality of the end product?
Metal-organic frameworks are known for their selectivity, ease of regeneration and cycle stability. These advantages come at a price, which is mostly above commonly used materials. Several studies have ventured into the cost structure of MOF production, mainly focused on manufacturing and material costs. While these studies certainly offer a valid insight into cost drivers and opportunities for improvement, it still does not take into account what benefit you gain from using these materials.
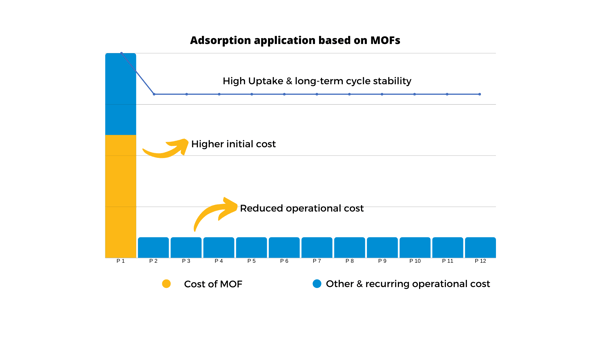
Using metal-organic frameworks in products that have used a replacement filter before might change the way your product is used. Maybe you just replace currently used material and tailor the regeneration method to fit. However, an economic view of any product development needs to take all parts into consideration – not just material price.
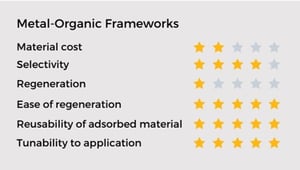
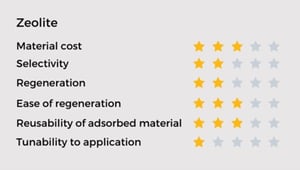
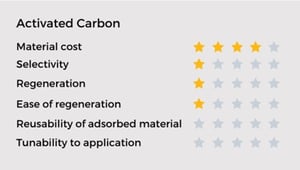
MOFs are not for everything
Every material has its limitations, and so do MOFs. The main limitations are high temperature and very low or high pH-levels. Then there are very MOF-specific limitations; some degrade in water or certain gases – while other MOFs adsorb water better than zeolites. Application of the specific material under adverse conditions would obviously make no sense for obvious reasons.
Certain MOFs have great catalytic or adsorptive properties, but their complicated building blocks or synthesis limit their commercial application. Even though they also offer long-term cycle stability and great regeneration, the benefit just doesn’t justify the elevated costs of the material.
Strong capabilities in improving unique applications
In other applications the unique composition of MOFs provides significant benefits. One example is the potential substitution of inorganic drug delivery agents for cancer treatment. While the treatment itself is already harsh on the body, the used materials have their drawbacks to. Treatment-specific tuned MOFs could offer higher biocompatibility, targeted delivery and controllable release patterns. All this together could significantly reduce negative side-effects and overall cost of treatment.
Purifying Krypton is an example of a high potential application of metal-organic frameworks. Krypton is usually purified by cryogenic distillation, which is a very energy-intensive process. Using the selective adsorption capabilities of MOFs could potentially reduce annual consumables cost to a third of the costs of cryogenic distillation. This is mainly due to the material stability beyond 500 expected adsorption/desorption cycles.
Offering new opportunities
We have talked extensively about improving existing products and processes. But the unique capabilities of MOFs offer new opportunities, that weren’t possible before.
Based on these porous materials, new products are developed that fulfill needs that haven’t been met before. Introducing new products also includes evaluating the value that they bring to the consumer. If the overall cost of the product (incl. a profit margin) match the value perceived by the consumer, it will be profitable for business.
Wrap up
In the end, it’s a question of the right material for the job – which might or might not be metal-organic frameworks. The decision to use or discard MOFs can’t be made solely on the price of the material itself but the overall benefit to the user. Thus, a thorough evaluation offers the chance to improve products or create new applications.