Gas separation is a critical process in many industrial applications, to either provide high purity gases or to capture harmful ones. Yet, many separation processes rely on energy intensive technology or on unselective approaches. The question is: are you ready to use MOFs?
In general, gases can be separated with three approaches: based on their intrinsic boiling point, their molecular size or their affinity to bind to other materials.
Fractional distillation: separation based on boiling points
Fractional distillation is the separation of feed components based on their distinct boiling points. The boiling point is the temperature at which a compound changes its state from liquid to gas, meaning until it vaporises every single molecule in the mixture.
Cryogenic distillation (fractional distillation at very low temperatures) is used for the large-scale separation or air into nitrogen, oxygen and partially argon. Other applications are the separation of liquid natural gas (LNG) and production of ultrapure gases (e.g. CO, argon, light hydrocarbons). At a large scale, this technology does work rather well for certain applications.
However, the cooling process requires vast amounts of energy, which is an environmental and financial factor to be considered.
Molecular sieving: separation based on molecular size
A molecular sieve is a porous material featuring pores of uniform size. These pores allow molecules under a certain size to enter, while others remain outside of the material. Micro-porous membranes are an example of size-specific separation. However, different mechanisms are used for the separation of the gases. If only certain molecules pass through the sieve, it’s called surface diffusion or molecular sieving. If some molecules take longer to pass the sieve as they are bigger than others, one can use the delay to separate the gases. This is called Knudsen diffusion.
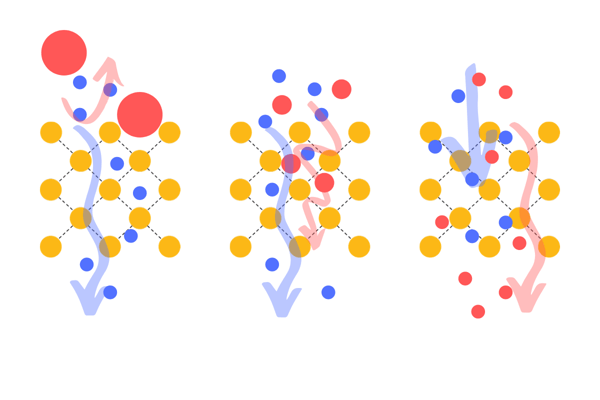
This picture shows different working principles of molecular sieves: Size-specific molecular sieve, molecular sieve with Knudsen effect and molecular sieve with adsorption of certain molecules /from left to right).
Relying only on molecular size for the separation brings some disadvantages; often separation does not produce pure gases, trade-offs in low selectivity/many separation stages, and high selectivity/few stages, fouling of the membrane and low throughput.
Furthermore, some molecular sieves use adsorption to bind the molecules within the pores.
Adsorption separation: separation based on binding forces
Some materials such as Zeolites, silica and activated carbon bind molecules to their surface. In chemisorption, the molecules are held by powerful chemical bonds and thus needs a chemical reaction between adsorbent and adsorbate. Physisorption relies on rather weak physical bonds between the molecules.
Either pressure swing adsorption (PSA) or temperature swing adsorption (TSA) setups are used to capture and release molecules from the adsorbent materials. Given the powerful bond in chemisorption, physisorption offers a significant advantage in the material’s regeneration.
New materials – new opportunities
The high energy penalty of fractional distillation and the disadvantages of membranes pushes researcher and companies towards other routes to separate gases. While zeolites, silica and activated carbon have been used in adsorption separation for several years, they have their restrictions.
Gas separations with MOFs: what works best?
When talking about MOFs in gas separations, we are always thinking of molecular size and adsorption behaviour. So what works best?
Is there enough size difference?
Given the porous structure of MOFs and the selectable building units, the first step would be to understand the size difference of the desired and undesired molecules. In other words: can we separate the gas mixture based on the molecular size? Tailoring the pore size of the MOF to accommodate one, but not the other molecule, and then build a membrane with it might do the trick. Another option would be to tune existing membranes with MOFs to increase their selectivity.
Membrane separation can be very useful in specific applications. However, to maximise the capabilities of the MOFs, adsorption separation should be evaluated in most cases.
Polarizability of the desired/undesired material
As mentioned above, combining molecular sieving and adsorption can be supportive to the separation. Adsorption in MOFs happens due to the (rather weak) Van-der-Waals forces and the polarizability of molecules. Tuning the MOF structure therefore offers the advantage of tuning the polarisation of the captured molecules and thus tailoring the adsorption behaviour. This leads to different binding energies for the same molecules in different MOFs. For example, for the separation of oxygen and nitrogen we would look for an oxygen selective MOF – as it’s the economically more desirable product. The MOF should not have too high bonding energy for easy regeneration of the oxygen and at the same time the least possible nitrogen bonding energy for highly selective separation.
To select the right MOF for your application, we would thus use the polarizability of each of the molecules and design the material around it.
Success in distinct applications thanks to MOFs
While the commercial application of MOFs is still very limited, they have proven to be very powerful in various gas separations. We had a look at some of these applications in earlies posts.
Oxygen generators
Current oxygen generators rely on the removal of the more abundant nitrogen (~78% of the air) rather than capturing the desired oxygen (~21% of the air). Highly selective metal-organic frameworks could turn this process around and provide highly pure oxygen with less energy-consumption and lower amount of material required. Read more.
Noble gas purification
Noble gas purification is an example of a cryogenic purification process, in which the energy consumption adds to the limited abundance of the gases. Light temperature swing adsorption processes could significantly reduce the amount of energy required for the purification. Read more.
But aren’t other adsorbents good enough?
Well, yes and no. Zeolites, silica and activated carbon are very capable in many applications. They have good selectivity and are quite robust in many environments. However, if you look for higher selectivity or selective pore sizes, you won’t get far with these materials. You get what’s out there.
If you are interested, read more in our comparison between MOFs and zeolites for gas separation.
MOFs, on the other hand, can be synthesised so they fit the application – from pore size to binding forces. However, given the more intense production of MOFs (in comparison to e.g. activated carbon), MOFs are more suited towards more specialised separations rather than bulk approaches.
Are MOFs the solution for your gas separation?
There is still no straight-forward answer to this. If you tick the following boxes, we would highly recommend evaluating MOFs:
- Separation based on boiling points is very energy-intensive
- Separation does not result in high-purity
- Size and/or polarizibility could be a separation feature, but common methods did not prove to be effective
This is a rough guideline, but we are happy to support you with additional information on your options based on your specific separation.